Die ersten Datensätze liegen vor, das Interface der Software wurde verbessert: Nach dem ersten Rollout im Herbst letzten Jahres hat das AW 4.0-Team wertvolle Erkenntnisse gesammelt. Jetzt startet Autowerkstatt 4.0 in die nächste Runde. Noch mehr Werkstätten erhalten erweiterte Messkits und umfangreichere Tests an weiteren Fahrzeugkomponenten sollen das Projekt voranbringen. Was genau das Team verbessert hat, welche Bauteile im Fokus stehen und welche Ziele das Team mit dem Rollout verfolgt, erfahren Sie im folgenden Blogbeitrag.
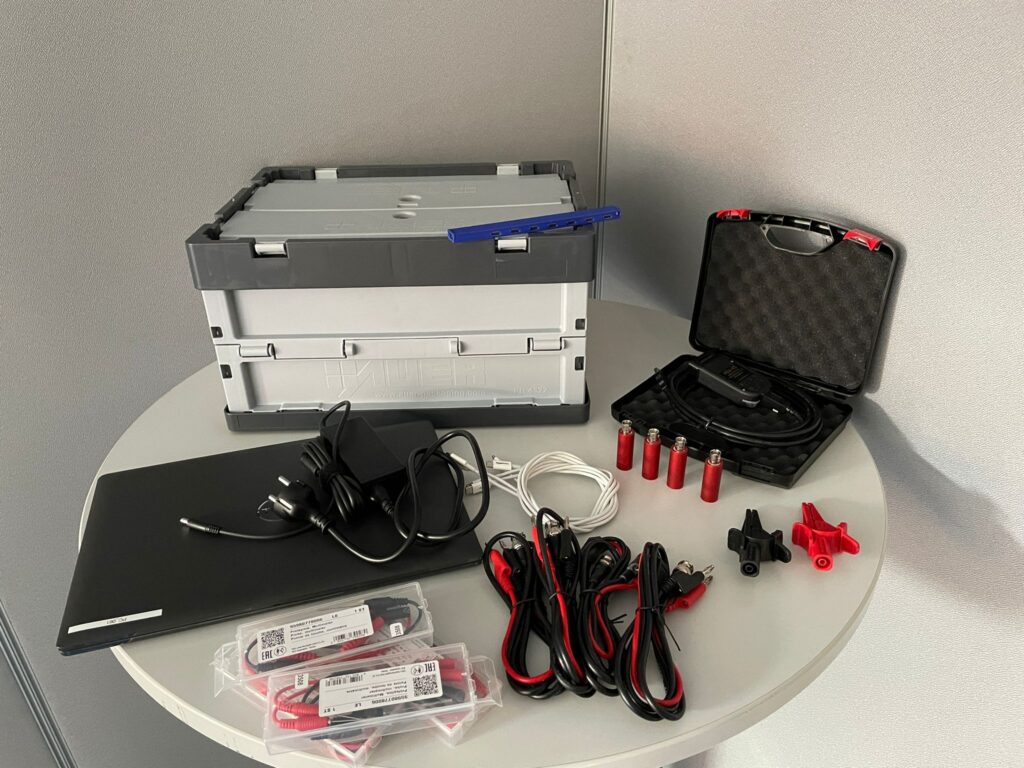
Ein Oszilloskop, ein VCDS und ein Messlaptop: Mit diesem Messkit stattete das AW 4.0-Team im Herbst vergangenen Jahres rund 50 Autowerkstätten deutschlandweit aus. Das Ziel: die im Projekt entwickelte Hardware und Software zur schnellen Fehlerdiagnose an Fahrzeugkomponenten zu testen und eine erste Datenbasis zu schaffen.
Mit den gewonnenen Daten soll der Forschungspartner Deutsches Forschungszentrum für Künstliche Intelligenz (DFKI) künftig eine künstliche Intelligenz trainieren, welches Fehler an Autobauteilen schnell erkennt und Lösungen vorschlägt. Ziel ist es, die Fehlersuche am Auto für Werkstätten mit Hilfe von Oszilloskopen und KI-gestützter Analyse einfacher und wirtschaftlicher zu machen. Eine deutschlandweite Plattform für den vertrauenswürdigen Datenaustausch von branchenspezifischen Fahrzeugdaten soll entstehen.
Erkenntnisse aus dem ersten Rollout
Der erste Durchgang ist beendet und das AW 4.0-Team konnte wichtige Erkenntnisse gewinnen. „Die Rückmeldungen der Werkstätten waren gemischt”, sagt Lukas Jakubczyk, Operativer Projektleiter im Wissenschaftsbereich Maschinenbau und Materialwissenschaften der Technischen Hochschule Georg Agricola (THGA), die die Werkstätten schult und betreut. „Die Euphorie war am Anfang sehr hoch. Aber viele Werkstätten berichteten uns von dem zusätzlichen Aufwand, den das neue System zunächst verursacht. Diesen Punkt können wir nachvollziehen, denn im täglichen Werkstattbetrieb bleibt kaum Zeit für außerplanmäßige Analysen.”
Dennoch: Nachdem viele Werkstätten das Messgerät und den Ablauf vor Ort selbst getestet hatten, waren sie von dem System angetan. Konkret haben sie im ersten Rollout die Batteriespannung beim Startvorgang des Autos als Messwert aufgenommen. Rund 100 Datensätze kamen dabei zusammen. „Das liegt zwar weit unter den 1000 Datensätzen, die wir benötigen, um die KI effizient zu trainieren”, sagt Jakubczyk. „Uns war aber auch von Anfang an klar, dass wir diese Datenmenge aufgrund der geringen Anzahl der teilnehmenden Werkstätten nicht erhalten werden.”
Trotzdem reichen die Daten aus, um eine erste Grundlage zu haben und die Usability des Systems zu verbessern. „Es ging uns primär um die Optimierung von Hardware und Software. Die Erfahrungen der Werkstätten sind sehr wertvoll für uns und die Weiterentwicklung des Projektes”, so Jakubczyk. Die gesammelten Daten hat die THGA bereits an das DFKI und die DEKRA DIGITAL weitergegeben. Diese haben die Daten synthetisch angereichert, also künstliche Daten hinzugegeben, damit die Datenmenge größer wird. Ein kleines KI-Modell ist daraus bereits entstanden.
Zweiter Rollout: Fokus auf Luftmassenmesser und Lambdasonde
Für den zweiten Rollout, der Ende Juli startet, stattet das AW 4.0-Team 20 Werkstätten hauptsächlich der Vergölst-Gruppe mit einem erweiterten Messkit aus. Das Feedback aus dem ersten Rollout hat das Team in der neuen Software berücksichtigt und etwa die Schriftgröße verändert und Farben hinzugefügt, um die Usability zu verbessern. Vor allem die farbige Anzeige der Graphen, wofür die Oszilloskope mit bunten LEDs ausgestattet wurden, ist ein praktisches neues Feature. „Der Graph auf dem Monitor hat jetzt die gleiche Farbe wie die Lampe am Messgerät”, erklärt Jakubczyk. „Optisch ist das eine deutliche Verbesserung im Vergleich zu den schwarzweißen Graphen aus der ersten Rollout-Runde. Das erleichtert das Ablesen auf dem Monitor und verbessert das Nutzererlebnis für die Werkstattmitarbeiter.”
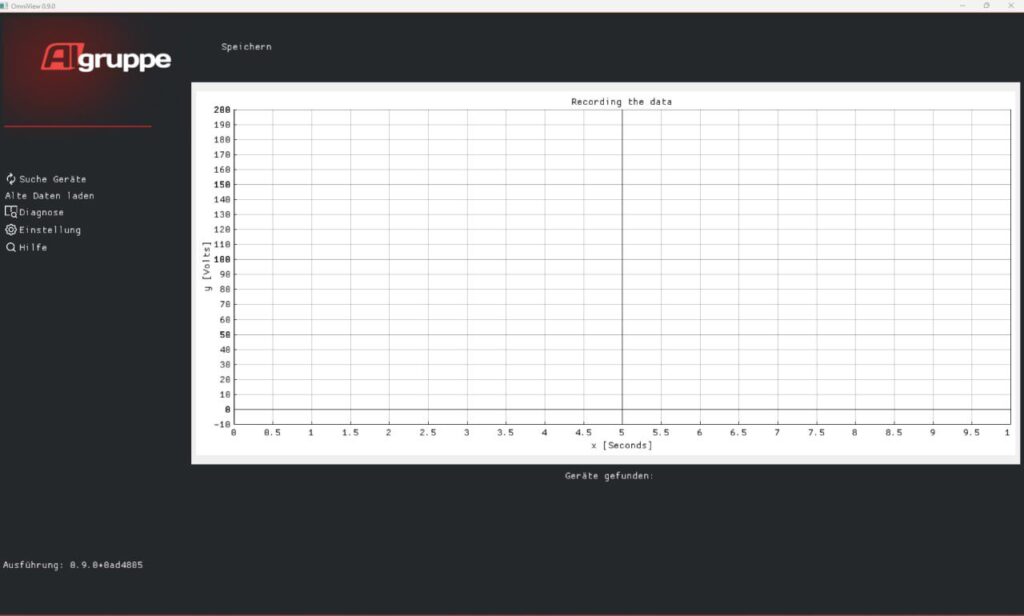
Auch der Fokus auf die Fahrzeugkomponenten ändert sich im zweiten Rollout. Haben die Werkstätten in der ersten Runde nur Daten rund um die Batteriespannung erfasst, liegt der Schwerpunkt nun auf dem Luftmassenmesser und der Lambdasonde. „Die Lambdasonde ist ein sehr komplexes Bauteil, das mit vielen Subsystemen in Verbindung steht, von denen bei einer Fehlermeldung rein theoretisch jedes defekt sein könnte”, sagt Jakubczyk. „Bei der Analyse entsteht ein riesiger Fehlerbaum und die Suche nach dem konkreten Problem ist langwierig.”
Der Fokus auf der Lambdasonde lohnt sich hier also besonders, um mithilfe einer KI schneller verlässliche Daten zu den Fehlerquellen zu erhalten. „Wir werden nicht wie beim ersten Rollout nur einen Messwert wie die Batteriespannung prüfen, sondern können direkt an zwei Sensoren jeweils zwei Messwerte erfassen”, erklärt Markus Kähler, Wissenschaftlicher Mitarbeiter an der THGA und Rollout-Manager. Die vier mit den Sensoren der Bauteile verbundenen Messgeräte sind über einen USB-Hub an das Notebook angeschlossen, sodass sich die Daten synchron aufzeichnen und analysieren lassen.
Schulung der Werkstätten vor Ort
Die teilnehmenden Werkstätten werden im Sommer von den AW 4.0-Experten vor Ort geschult. Wie beim ersten Rollout wird das Team das Messkit vor Ort vorstellen und gemeinsam mit den Werkstätten erste Messungen durchführen. Rund zwei Stunden dauert so eine Schulung. Auf einer eigens entwickelten Lernplattform können die Werkstätten das Gelernte nochmal nachlesen oder in Videos anschauen, wie Hardware und Software zu nutzen sind.
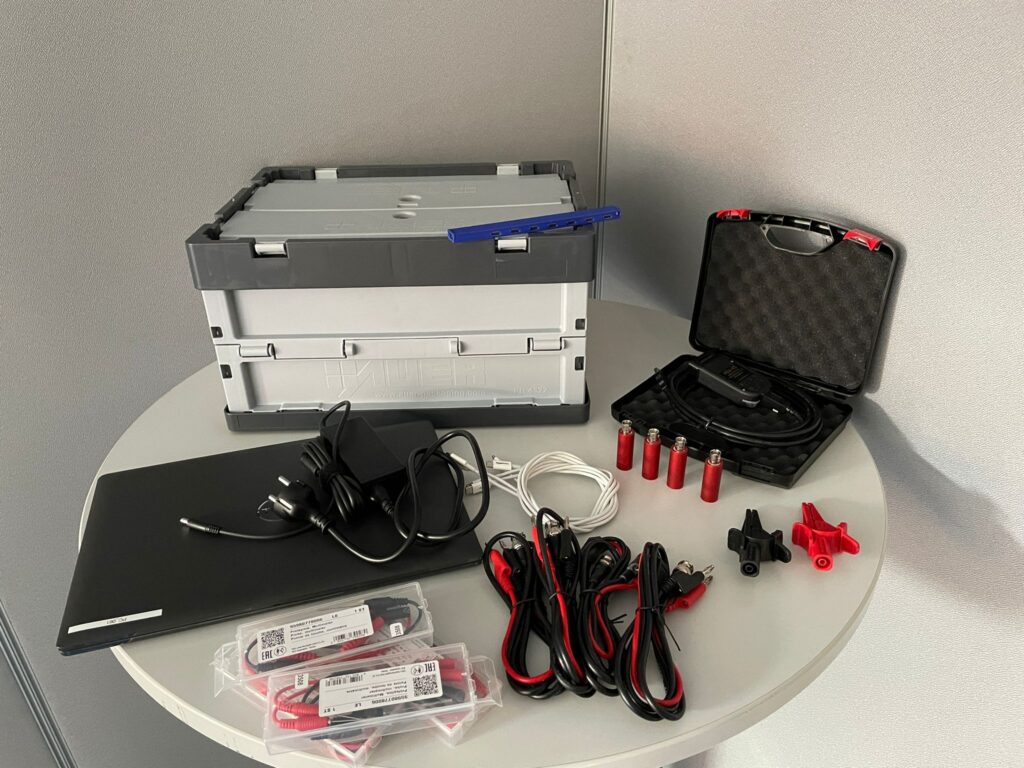
Mit dem zweiten Rollout erwartet das AW 4.0-Team eine größere Datenbasis, die das DFKI und DEKRA DIGITAL analysieren und anreichern können. Der zweite Rollout soll deutlich umfangreichere und qualitativ hochwertigere Daten liefern. „Ich würde mich freuen, wenn die Werkstätten das Messsystem über den Rollout hinaus in ihren Arbeitsalltag integrieren und es zu einem festen Bestandteil ihrer Diagnosewerkzeuge wird”, sagt Kähler. „Denn auch ohne KI ist das System bereits eine große Hilfe für Werkstattbetreiber, um Fahrzeugmessdaten visuell ansprechend aufzubereiten.” Langfristig gesehen sollen die Daten in die Gaia-X-Infrastruktur integriert werden, um eine breitere Nutzung und Weiterentwicklung der Fahrzeugdaten zu ermöglichen.
Das sagt die THGA:
„Wir alle wissen, dass Daten das neue Rohöl sind. Mit unserem Oszilloskop und der Daten-Pipeline ermöglichen wir den Werkstätten dieses zu fördern. Wir sehen dies als eine Anlage in die Zukunft.”