In December, Car Repair 4.0 carried out measurements on vehicles at a Vergölst branch in Bochum. The aim was to record the voltage of a battery during the starting process of a car and to test data transmission and data management. The Car Repair 4.0 measurement team hopes to gain important insights from the standardised procedure. The data will be used to train initial networks and evaluate the procedure.
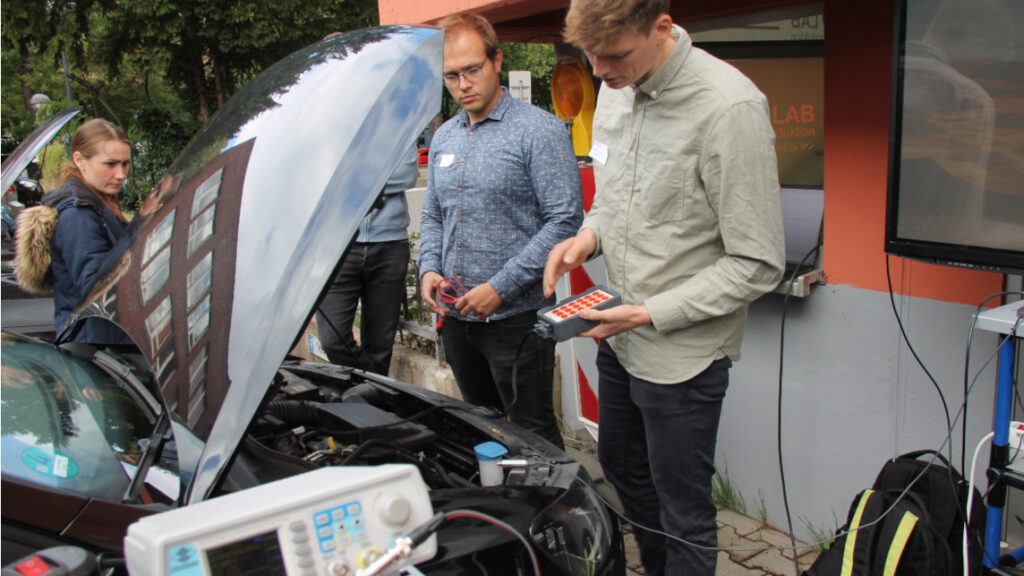
By Ralf Schädel, IT Editor and Project Manager Cloud Services and Gaia-X at eco – Association of the Internet Industry
In order to ensure that the collected data is comparable in a decentralised measurement in different car repair shops, the same conditions must always prevail. That’s why the measurement professionals from Car Repair 4.0 have created and standardised a simple data acquisition process for the battery of a diesel car, which transmits high-resolution data directly to a server or the cloud. The test setup should allow many conclusions to be drawn that could be of great importance in the further course of the project.
Measuring components and infrastructure are checked
“We hope to be able to use the method to test the measuring computer and its software for functionality. In addition, the resulting data will put the functionality of the data infrastructure to the test and generate data sets for training purposes,” explains Magnus Komesker, research assistant at Osnabrück University of Applied Sciences.
Measuring the battery using an oscilloscope is ideal
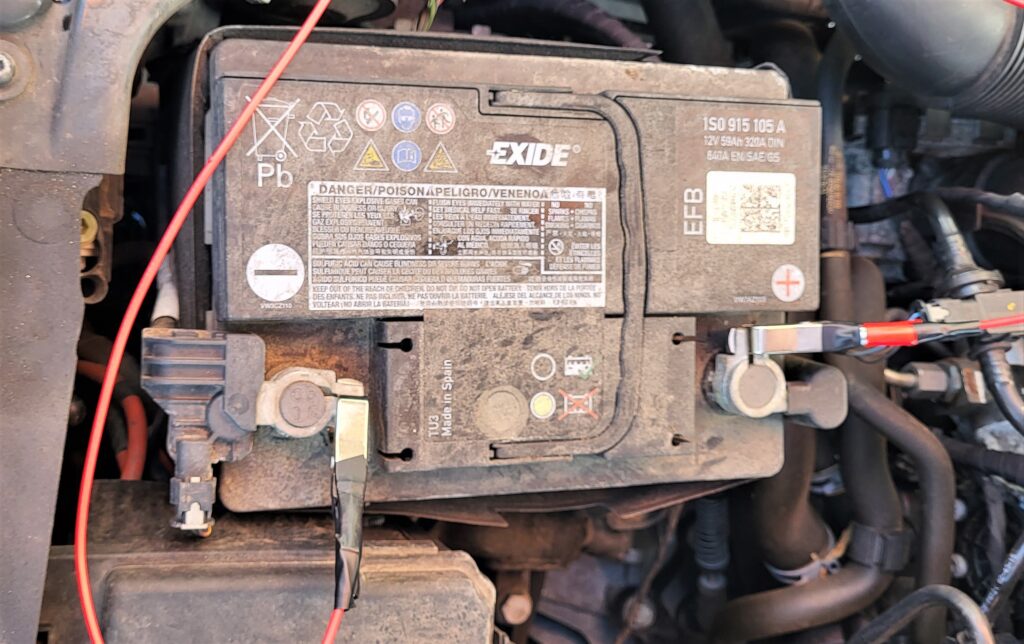
Why was the method of standardised battery voltage measurement chosen? The connection points are easy to reach and the battery serves as a good visual example. This is because the voltage curve of the battery during the starting process is influenced not only by the battery itself, but also by several components. “We expect to gain a lot of information from battery measurement using an oscilloscope, which we can only obtain to a limited extent via the OBD connector,” says Komesker. For example, minor deviations may not be detected by an OBD device or error codes may not be filed. An oscilloscope measurement on the battery, on the other hand, yields a high-resolution signal that reveals, among other things, the firing of the cylinders, the charging curve when the alternator is switched on, and other important factors.
Blueprint with savings potential
“The connected battery in the idle state provides information directly via the volt number as to whether it is healthy or not,” says Bastian Kuhle, research associate at the Georg Agricola University of Applied Sciences. When the ignition is started, you can see how the starter motor has to work against the compression of the engine and the voltage on the battery drops, according to Kuhle. The information obtained here about the cylinders’ compressions is recorded in just ten seconds – a conventional compression measurement in the car repair shop takes around half an hour. Such a voltage measurement also serves as a blueprint: It generally allows one to draw conclusions about mechanical components. Defects in components can thus be identified more quickly and accurately, saving significant resources for the car repair shop.
This is how data transmission works during measurement
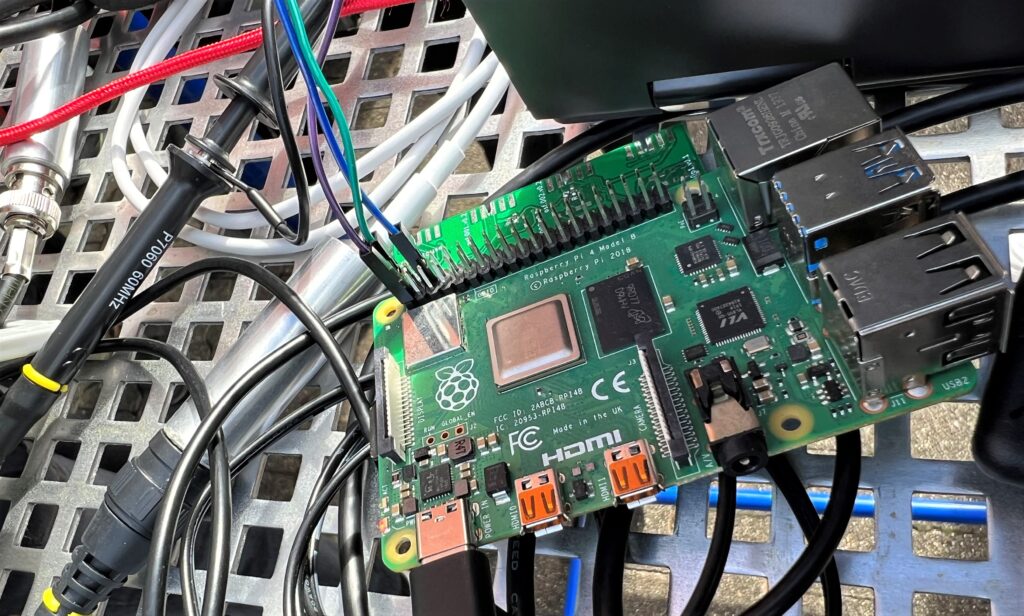
The data is recorded with a so-called Raspberry Pi, a single-board computer. After the vehicle data such as type and year of manufacture have been entered, all that needs to be done is to click on “Start measurement”. When the vehicle is switched on, the computer records the voltage curve that is present in the battery during this time and sends it automatically to the server. This data is first used to train the neural networks, which will provide a solution design in the long term. The solution is then transferred to the mechanic in the car repair shop with a clear recommendation for action in the future data process, so that the mechanic is guided step by step to the solution.
New connections facilitate data recording
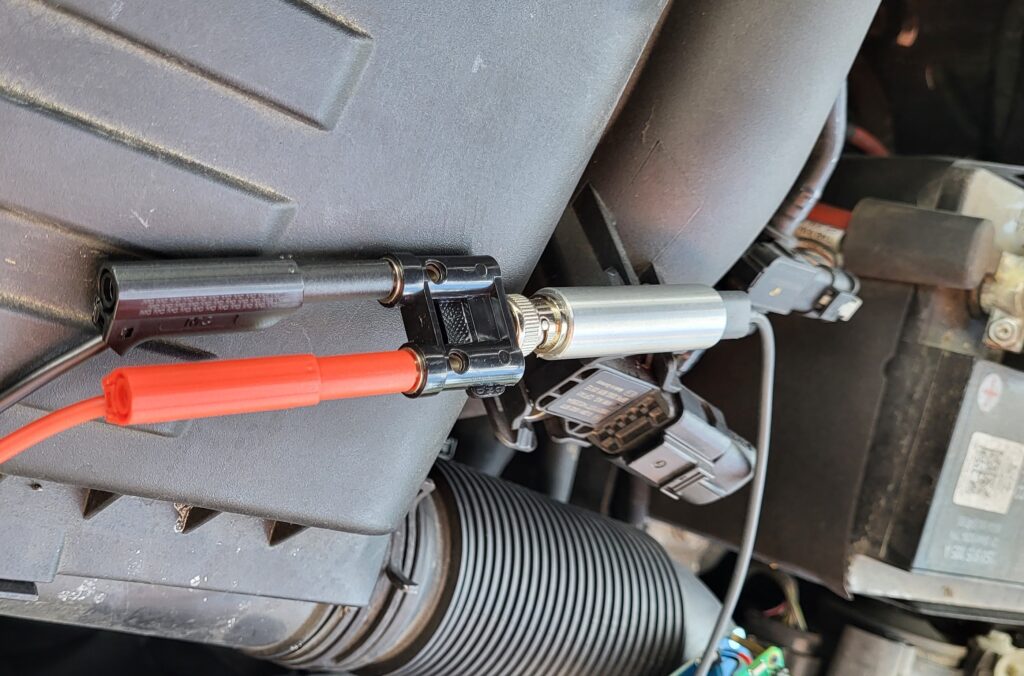
Since manufacturers’ connections for sensor acquisition are always changing, which makes it harder for the mechanic to record signals, Car Repair 4.0 is addressing this issue. The first solution is a Y-connector. In the long term, a clothes peg-like plug is planned. It offers the advantage of being minimally invasive. Connections that are difficult to reach in the engine compartment then do not have to be exposed at great expense. Instead, live cables can be “listened to” directly – without being damaged.
The more accurate the input, the better the solution
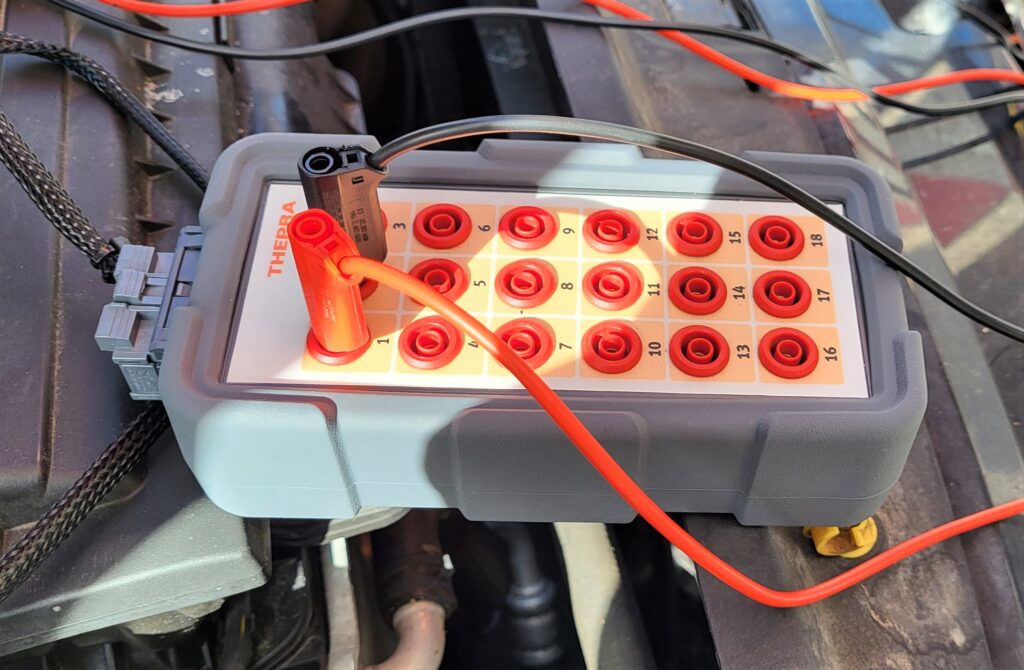
To obtain a comparison signal via individual sensors, the experimental setup provides for the breakout box. It ensures that, analogous to battery measurement, several data can be compared with each other and thus insights into the faulty behaviour of a sensor can be gained. “We play through different scenarios here: for example, that the sensor works perfectly or that there is a basic error. These different signal images must be compared with the algorithm in order to be able to offer the car repair shop clear solutions,” says Kuhle.
Car Repair 4.0 is not quite there yet, but the standardised battery measurement is the next milestone on the way to AI-supported fault diagnosis!
Did you enjoy reading this article? Then subscribe to our newsletter and receive regular updates on related topics and on the Car Repair 4.0 project, and discuss this and similar exciting topics with us on LinkedIn.