The “Sunrise” conference room of the DE-CIX MeetingCenter in Frankfurt was filled to capacity. The Who’s Who of the automotive and supplier industry had accepted the invitation of eco – Association of the Internet Industry and Car Repair 4.0: At the workshop “How data and AI transform car repair shops”, participants discussed their practical experiences with data pots, silos and streams with great dedication and commitment and agreed on the necessary willingness to share data. In a series of short pitches, working groups presented their visions of the car repair shops of the future.
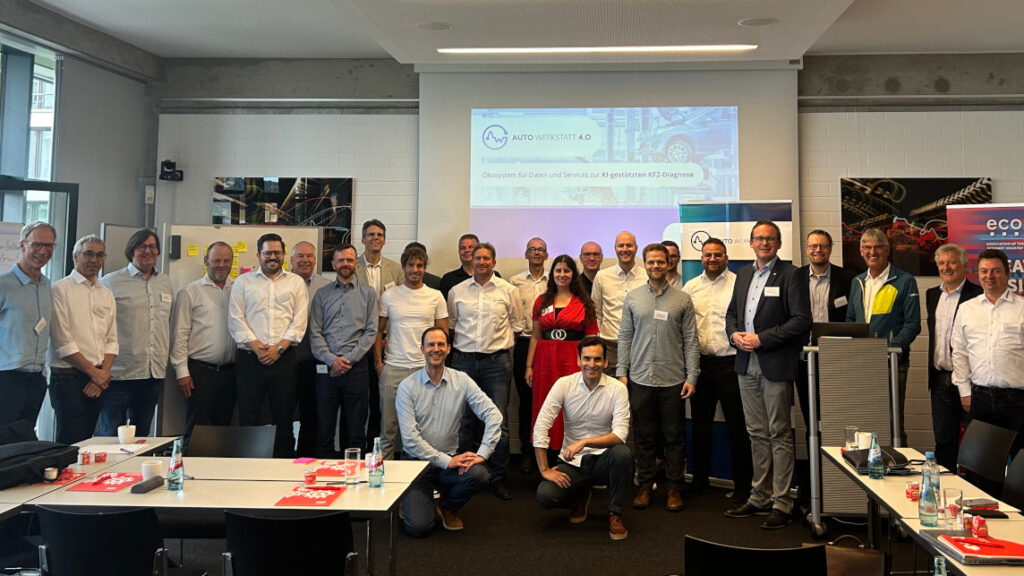
By Ralf Schädel, IT Editor and Project Manager Cloud Services and Gaia-X at eco – Association of the Internet Industry
Data is the innovation driver of the automotive industry and modern garages. If you want to develop new business models and explore untapped business areas, you need to understand product and data cycles. This is th only way to offer customers better and more sustainable services. This was emphasised by the representatives of Germany’s most renowned suppliers, service providers, associations and institutes at the Car Repair 4.0 workshop. In exciting discussions, they exchanged ideas on topics such as access to data and its shared use and monetisation with a great deal of expertise and commitment. Socio-political issues such as the lack of skilled workers and economic aspects such as securing the future of the German automotive industry were also discussed.
Gaia-X and Car Repair 4.0 focus on data sovereignty
The two speakers Jan Hendrik Schoenke, Head of Research and Development at consortium leader LMIS, and Juan Hahn, who acts as Partner and Business Development Consultant on behalf of the Car Repair 4.0 consortium, explained the importance of a secure and trustworthy ecosystem like Gaia-X and its lighthouse projects. “Projects like Car Repair 4.0 are a piece of the puzzle to make data sharing tangible for business,” said Schoenke. Certifiable and centralised models according to Gaia-X standards enable the regulation of data, while ensuring the data sovereignty of OEMs and customers. Data processing can also take place in car repair shop hubs, scalable units within the Gaia-X ecosystem.
Actual and target state for data sources
Together, the participants examined the current state of data sources in the companies. The focus was on key questions about the current data situation and the procurement of vehicle data – as well as possible hurdles and the consequences for everyday car repair shop work. The experience: The exact identification of the vehicle and the components often proves to be challenging. The market for diagnostic tools and software is large, but not all tools produce the same results. In this respect, the knowledge that is available at car dealers and car repair shops cannot be shared and used in a structured way.
Often, only car repair shop floor managers have access to diagnostic equipment, as the manufacturers’ personalised licences are expensive and smaller car repair shops can only afford one. The cost-benefit ratio of data use is therefore a major issue. The level of knowledge, training and further education of car repair shop staff in relation to diagnostic tools and services was also criticised. The diagnostic result reflects the knowledge of the master mechanic, who has not even searched the Internet, and there is no exchange of information between colleagues – nor is there manufacturer and vehicle data, historical repair and customer data, experience reports or customer discussions.
Visions of the car repair shop of the future
How could the digitalised car repair shop of the future position itself better? And which financial resources, service offerings, customer experiences, implementation speeds or sustainability criteria play a role? These were presented by the working groups in short pitches. The ideas and visions focused, in particular, on customer benefits: In this context, time and money will play an even more existential role. The aim is to minimise the time burden on customers and to provide them with as reliable a forecast as possible of how long they will have to do without their vehicle.
Unrestricted access to data and functions as well as a system for data management underpin this vision. The use of data would need to meet international standards and training and education should find solutions for the shortage of skilled workers. Virtual and augmented reality could play an increasingly important role in this, providing precise offers of assistance in diagnosis. According to experts, predictive maintenance in conjunction with AI will be a key issue: in the future, vehicles will communicate even more with people and the environment and, in the best case, will be able to tell what they are missing or what they need.
Whether the repair solution is mobile or on-site, spare parts or special tools for the repair can be ordered in advance. The “car repair shop 4.0” can plan and work more efficiently for the benefit of the customer – as well as take sustainability into account by reducing material usage and saving on carbon emissions. Longer product life cycles not only pay off directly in terms of sustainability, but also are changing the parts market. Even the use of 3D printers or drones is conceivable. Full payment and insurance processing would round off the 360-degree service for customers.
Insights and feedback from workshop participants
For the participants, the workshop not only provided an opportunity for creative exchange, but also for information: Frank Mauder from ZF Aftermarket found it exciting to learn about the views and further developments of other companies in the industry. “For us, I see a great opportunity to offer added value to the customers and car repair shops we serve in the future.” Dr. Tobias Schweickhardt from Daimler Truck AG wished to get an overview of the current political discussion regarding the Data Act and access to vehicle-generated data: “The debate is sometimes conducted in too abstract a manner and only in buzzwords. In the workshop, I was able to gain insights into use cases at car repair shops, service providers and customers of vehicles, which also help our company.”
Ludger Kersting, Managing Director of ADAC Service GmbH, positively highlighted the fact that access to data, in particular, was addressed in the workshop: “The industry does not provide us with enough data as a service provider, although this significantly improves the service of the future customer industry on the road.” In the workshop, as Kersting continued, there was significant interest expressed from various parties in disclosing and sharing data. “For car repair shops and all those working in the service sector,” he said, “a world must open up in which we think and act together in the interests of the customer.” The major difficulties still lie with the vehicle manufacturing industry – not with the suppliers,” notes the ADAC expert. Without the willingness to share data, the industry in Europe would have clear competitive disadvantages compared to companies in the USA and other continents.
Conclusion and appeal
Independent car repair shops are also at a disadvantage in the market if they do not recognise the first AI-assisted error diagnosis measurements as part of the upcoming Car Repair 4.0 rollout as the starting signal for a new future. The workshop participants agreed that a support project like Car Repair 4.0 can trigger a domino effect. The first car repair shops are joining in, and others are following suit in order to further digitalise, align their service portfolio with customer needs and a sustainable value chain, and thus keep pace with the competition. It is undeniable that, in order to efficiently drive transformation and data use in the future, it is necessary to work together. That is why the workshop participants used the opportunity to network beyond the exchange of ideas.
Did you like this article? Then subscribe to our newsletter and receive regular updates on similar topics and on the Car Repair 4.0 project and discuss this and similar exciting topics with us on LinkedIn.